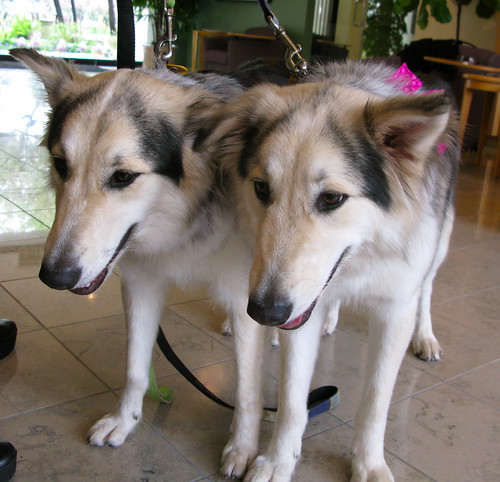
I have blogged here several times about the tension between innovation and reuse (see here, here, here) and concluded that "The secret, and our aim as professional knowledge managers, is to ensure that people reuse knowledge wherever knowledge is well established, and are creative and innovative where there is room to be creative and innovative".
Here's a story from BP that takes this thought further, and puts some numbers to the value generated.
I was in BP yesterday, and picked up a copy of their internal "Horizon" Magazine that they supply to staff, contractors and visitors. It had a really interesting article on Standardisation, and the benefits that this can bring when combined with KM. This magazine is not published online, so I won't reproduce it in full here, but I will extract a couple of key points.
BP often finds itself in a position where it needs to do things several times. Maybe they build several gas stations in Germany, or build several LNG trains in Angola, or build several offshore platforms in Trinidad. Their philosophy nowadays is "to take a blueprint and tweak only where necessary, instead of recast the mould every time". In other words, they clone and improve, clone and improve.
The article quotes one of BPs chief engineers as saying ""That does not preclude the option to change and there are certainly times when you do need to innovate, but we need to be changing only where it is of value. You have to ask; where do you get real advantage in change, because 90% of the time, we think advantage is illusory, and change costs more."
Very interesting. 90% of the time, change costs more and the value is illusory.
When the article starts to quote figures, though, you can begin to see the value. Take the thee Trinidad platforms, where the second and third were clones of the first. The project time for the first was 34 months, 29 months on the second, and 24 months on the third. The platforms were identical, but the performance got better and better, and the build time got shorter and shorter.
SO how can this be? If they are identical, then why didn't they take the same length of time to build?
This is where KM came in. Each project was operated with KM as part of the operation philosophy. Each project collected lessons, and applied lessons from the past, and each time this allowed a significant drop in manhours per platform as each facility was designed and built. In effect, they delivered a learning curve.
Standardisation brings other benefits, such as the long-term relationship you build with the contractor, and the savings on spares, but the ability to learn and re-use is a massive, massive benefit. If each platform had been different, then each one would have started all over again at the head of the learning curve.
There's another BP article, this time available online which mentions the standardisation approach, and talks about how this approach has speeded up the delivery of platforms in Azerbaijan, cut costs, and accelerated the delivery of oil. According to the online article (my emphasis),
"The Phase 1 Central Azeri (CA) production platform .... delivered first oil six weeks ahead of schedule. In Phase 2, West Azeri (WA) is expected to come onstream before the end of this year, well ahead of its original April 2006 schedule, while East Azeri (EA) could shave at least four months or more off its original planned start date of February 2007........Measured by the industry yardstick of design manhours per tonne of topsides, facilities engineering on the CA ‘prototype’ came in at 42 manhours per tonne. WA took this down to 31 manhours, and for the identical EA this fell even further to 11 manhours per tonne.
‘These savings translate into tens of millions of dollars for the project,’ Brown observes. ‘Furthermore, the number of engineering change requests – often the bane of successive offshore projects – fell by more than half, as did the queries coming from the construction sites as the fabrication teams gained familiarity with repeat
structures and items of equipment.’
To reach that positive outcome, activities in each phase of the project – design, procurement, fabrication, transportation, installation and commissioning – require meticulous planning, plus an effective process for sharing lessons learned, and a disciplined approach to sticking to the standardisation mantra of cloning between successive platforms".
And one point about that "effective process for sharing lessons" - the magazine article mentions transfer of knowledge from one project to another in Azerbaijan, where 700 lessons were identified on one project, of which 400 were re-used on the next.
I would just like you to reflect for a moment on those figures.
Firstly - 700 lessons from a project. OK, it was a big project, but how many times have you heard people say "Just give me the top 3 lessons - the top 10 lessons". No - if 700 important things have been learned, let's have all of them!
Secondly - 400 out of 700 were re-used. That's nearly 60%. I wonder what percentage of your project lessons get reused, dear reader?
I was really pleased to see this article. I know BP is a very innovative company, but here's a really pragmatic approach to reining in the risk of "Innovation in the wrong place", and instead delivering the value that comes from a strategic approach to standardisation linked with KM and project-based lesson-learning.
2 comments:
Had to read it a few times to really get the depth of the points you're trying to make. I think this is a very important question - "what percentage of your project lessons get reused" ... we reuse often, but it is always a small percentage of lessons that can be reused.
Thanks Sam. I know that "reusing lessons" is a means, not an end, but the story here shows how by using the clone concept, massive learning and improvement can take place. I worked with another company who were installing many offshore wellhead platforms on one of their fields. Each platform was commissioned separately (often from a different contractor) and as a result there was almost no opportunity for learning, and no trend of reducing costs.
Post a Comment